Firmy TorqSmooth Transmissions oraz Aluminium Parts toczą spór w kwestii reklamacji jakościowych dotyczących pierwszej wyprodukowanej partii wyrobów, będących korpusami mechanizmu różnicowego AWD nowej przekładni bezstopniowej CVT, produkowanej przez firmę TorqSmooth i przeznaczonej do pracy pod średnim obciążeniem.
Kontrola dostaw w firmie TorqSmooth odrzuciła partię 3000 korpusów, twierdząc że 24% z nich nie spełnia specyfikacji tolerancji pozycji otworów z luzem pod elementy złączne. Wyrywkowo skontrolowano 30 sztuk, wśród których wykryto niezgodności. W związku z tym sprawdzono większą próbkę a uzyskane wyniki potwierdziły początkowe ustalenia. Na tej podstawie specjaliści jakości firmy TorqSmooth oszacowali, że zdolność procesu Ppk w zakładzie dostawcy, uzyskiwana dla pozycji otworu kołnierza montażowego wynosi jedynie 0,24. Jest to zdecydowanie poniżej minimalnego poziomu Ppk, który zgodnie z wymaganiami PPAP powinien wynieść co najmniej 1,67. Taki wynik jest również zbyt niski w stosunku do oczekiwanego poziomu zdolności w bieżącej produkcji seryjnej wynoszącego 1,33.
Z drugiej strony w dokumencie PSW firmy Aluminium Parts stwierdzono, że specyfikacja tolerancji pozycji była sprawdzana w co dziesiątym wyrobie za pomocą „sprawdzianu funkcjonalnego”. Zgromadzone wyniki kontroli wykazały brak jakichkolwiek niezgodności w zmierzonych sztukach. Mimo to TorqSmooth na podstawie własnych pomiarów podjęła decyzję o odrzuceniu komponentów i zażądała od Aluminum Parts odebrania wadliwych części oraz zastąpienia ich częściami zgodnymi. Firma Aluminium Parts, przekonana o poprawnym działaniu swojej kontroli jakościowej, postanowiła ponownie skontrolować 300 sztuk z dostarczonej partii. Weryfikacja została przeprowadzona w zakładzie klienta, ale z wykorzystaniem sprawdzianów produkcyjnych dostawcy. Ponownie nie stwierdzono żadnych niezgodności. Brzmi znajomo?
Czy kiedykolwiek zastanawiałeś się, dlaczego sprawdziany pozycji, które wykorzystujesz w swoim procesie, dają wynik „zgodny” dla praktycznie wszystkich wyrobów, podczas gdy analiza SPC przeprowadzona na podstawie uzyskanych danych pomiarowych wskazuje, że znaczna część z nich powinna zostać odrzucona? Ta rozbieżność nie wynika z braku porównywalności technik pomiarowych – ze stosowania w jednym przypadku danych ciągłych a w drugim atrybutywnych. Jest ona raczej skutkiem odnoszenia zmienności produktu do różnych przedziałów specyfikacji. Sprawdziany tolerancji pozycji generują dane dyskretne (zgodny-niezgodny) poprzez weryfikowanie cechy pozycji z jej najgorszym przypadkiem ograniczenia fizycznego, uwzględniając jednocześnie ograniczenia wymiaru otworu i pozycji, podczas gdy w pomiarach ciągłych wymiar i pozycja są rozpatrywane oddzielnie, każdy w odniesieniu do swoich granic specyfikacji.
Specyfikacja otworu

zawiera modyfikator tolerancji nazywany stanem maksimum materiału MMC (Maximum Material Condition). Oznacza on, że gdy wymiar otworu osiąga stan maksimum materiału (czyli najmniejszą średnicę otworu Ø 8.91), wówczas jego granicą tolerancji geometrycznej pozycji jest wartość Ø 0.36.
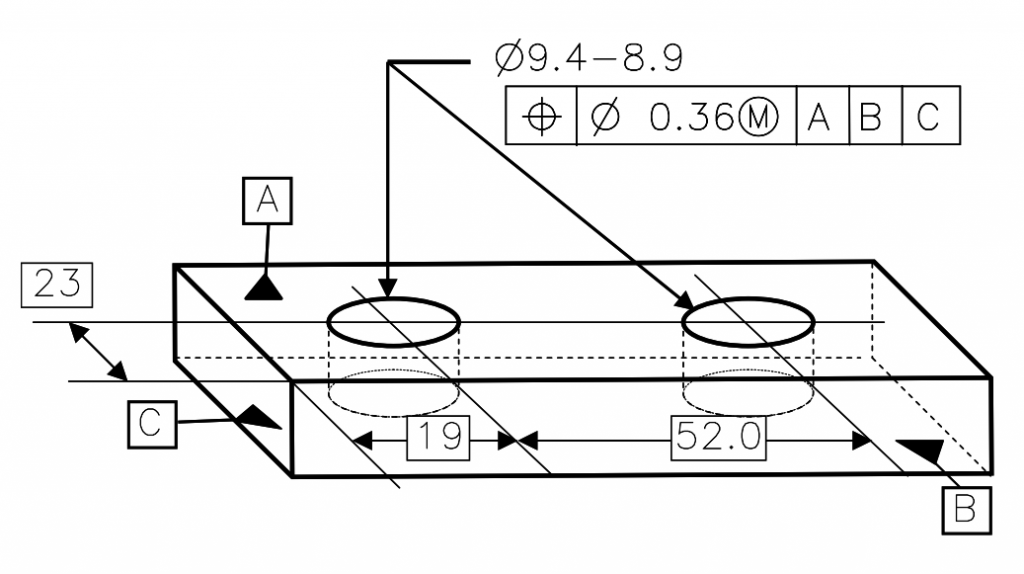
Gdy wymiar otworu rośnie, odpowiednio rośnie również geometryczna tolerancja pozycji, ponieważ położenie większego otworu może bardziej odbiegać od wartości nominalnej (ze względu na pojawiający się luz) niż położenie otworu mniejszego, w dalszym ciągu pozwalając na przejście elementu złącznego przez gwintowany otwór. Gdy otwór osiąga największą średnicę Ø 9.4, jego tolerancja geometryczna wzrasta do maksimum wynoszącego Ø 0.86, co równa się Ø 9.4 USLS – Ø 8.9 LSLS + Ø 0.36 USLP, gdzie USLS i LSLS to odpowiednio dolna i górna granica specyfikacji wymiaru otworu, natomiast USLP, to górna granica specyfikacji tolerancji pozycji.
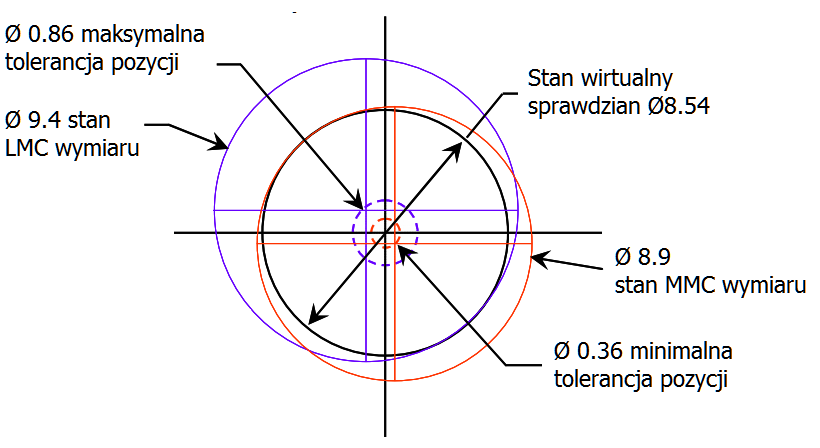
Sprawdzian atrybutywny firmy Aluminium Parts jest wyposażony w kołek o średnicy Ø 8.54, co odpowiada „stanowi wirtualnemu” (virtual condition) lub wewnętrznej granicy otworu Ø 8.9 (Ø 8.9 MMC lub LSLS minus Ø 0.36 USLP). Sprawdzian został więc tak zaprojektowany, aby otwór o średnicy Ø 8.9 i przesunięty o 0.36 dawał pozytywny wynik sprawdzenia. Średnia średnica mierzonych otworów wyniosła około 9.13 mm, a więc średnia zmienna tolerancja pozycji próbki zbadanej na sprawdzianie wyniosła około Ø 0.59 (USLP Ø0.36 + XS Ø9.13 – MMCS Ø8.9). Oczywiście każdy otwór miał inną wartość tolerancji pozycji, zależną od jego średnicy, ale każda sztuka przeszła ocenę zgodności na sprawdzianie.
Inspektor kontroli dostaw w firmie TorqSmooth sprawdził wymiar i pozycję tych samych części za pomocą maszyny współrzędnościowej, przedstawiając dane na oddzielnych histogramach – osobno dla wymiaru i osobno dla pozycji – a następnie wyznaczył współczynniki zdolności dla każdego z tych zestawów danych. Zapytajmy więc jeszcze raz, dlaczego zdolności procesu obliczone przez TorqSmooth tak bardzo odbiegają od wyników uzyskanych na sprawdzianie firmy Aluminium Products? Uzyskane wyniki analizy zdolności obrazuje poniższa tabela:
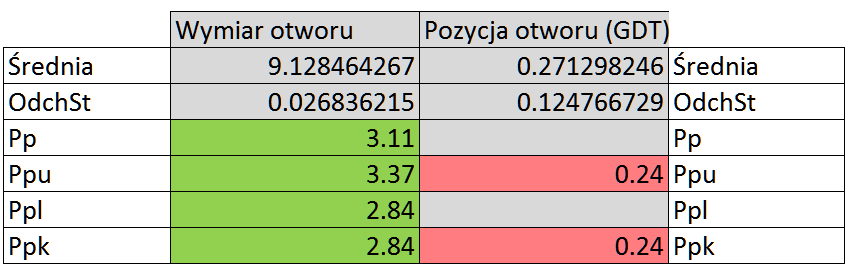
Wygenerowano również histogramy odzwierciedlające zmienność obu charakterystyk:
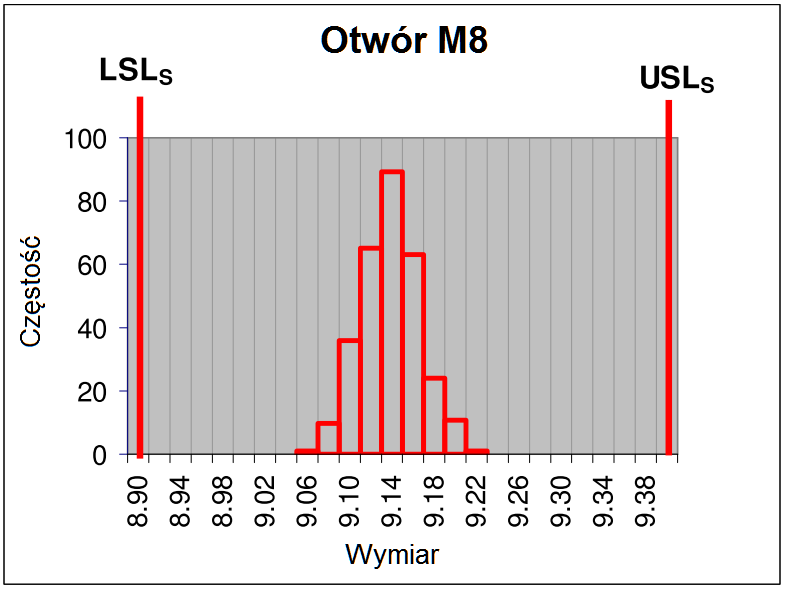
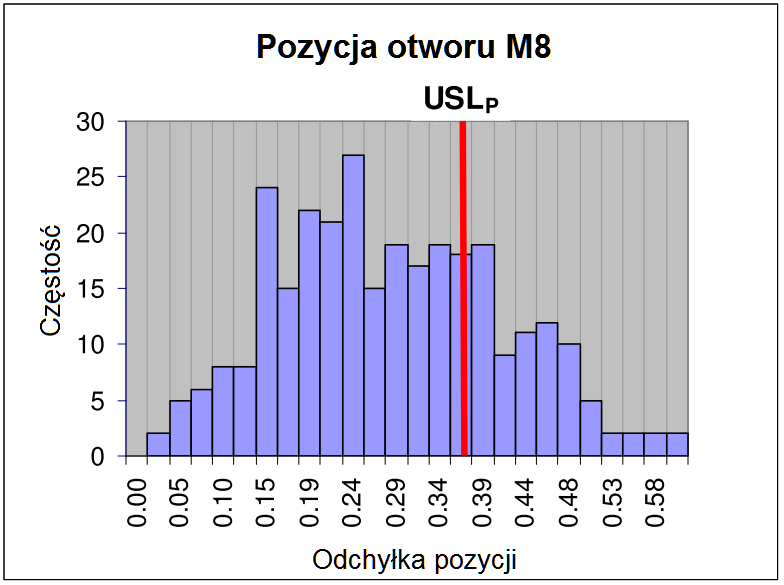
Odpowiedź jest następująca: równanie zastosowane przez TorqSmooth do oceny zdolności dla pozycji otworu traktuje górną granicę specyfikacji (USL) jako stałą wartość i ignoruje zmienny „bonus” tolerancji. Z kolei Aluminium Products wykorzystała w pełni zmienną tolerancję, wprowadzając zmienny fizyczny „bonus” w swoim sprawdzianie atrybutywnym. Tak więc aby prognozy dotyczące zdolności procesu były zgodne z wynikami uzyskiwanymi na sprawdzianie, koniecznie jest uwzględnienie w tych wyliczeniach zmiennej części tolerancji.
Współczynniki statystyczne, takie jak Pp/Ppk oraz Cp/Cpk są powszechnie wykorzystywane do porównywania zmienności procesu z granicami specyfikacji. W ten sposób można wyznaczyć potencjał i zdolność na podstawie pomiarów ciągłych z próbki pobranej z procesu produkcyjnego w jakimś okresie czasu. Gdy proces jest przewidywalny, a więc gdy występują w nim tylko ogólne przyczyny zmienności, nazywamy go procesem „sterowalnym”. Możliwe jest wówczas oszacowanie wydajności procesu za pomocą następujących równań:

Powyższe formuły mają zastosowanie w przypadku rozkładu normalnego oraz stałych granic specyfikacji. W przypadku granic dwustronnych rzeczywista zdolność procesu (Ppk) staje się równa zdolności potencjalnej tego procesu (Pp), jeżeli średnia rozkładu jest wyśrodkowana pomiędzy dolną (LSL) i górną (USL) granicą specyfikacji. Z kolei w przypadku granic jednostronnych zdolność procesu wynika z ryzyka przekroczenia tylko jednej granicy (LSL lub USL). Wówczas zdolność potencjalna Pp jest zwykle pomijana, ponieważ przewidywanie, jaka część rozkładu przekroczy granicę oznaczającą wartość idealną, zerową odchyłkę lub wartość nieskończoną, jest bezcelowe z punktu widzenia badania prawdopodobieństwa wystąpienia wady.
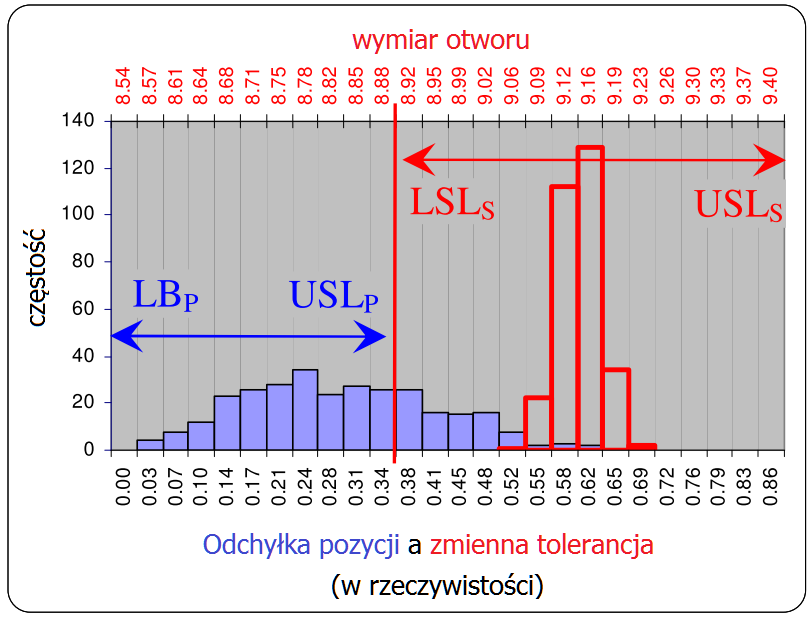
Związek między cechą wymiaru a zmienną tolerancją Ø8.9 MMC = Ø0.36 MIN oraz Ø9.4 LMC = Ø0.86 MAX może być przedstawiony graficznie za pomocą zachodzących na siebie rozkładów (oddzielnie dla odchyłki pozycji i wymiaru otworu) – przedstawionych na tym samym histogramie w taki sposób, że ich przedziały tolerancji przylegają do siebie. Na rysunku widzimy, że „stan wirtualny” pokrywa się z wartością 0 dla tolerancji pozycji, stan MMC (maximum material condition) lub LSL wymiaru wynoszący 8.9 pokrywa się z wartością MIN zmiennej tolerancji pozycji wynoszącą 0.36, natomiast stan minimum materiału LMC (least material condition) lub USL wymiaru pokrywa się z wartością MAX zmiennej pozycji tolerancji wynoszącą 0.86.
Przedstawiony na poniższym rysunku klasyczny model rozkładu niezawodności, uwzględniający naprężenie i wytrzymałość, odzwierciedla analogiczną relację między wymiarem a pozycją, dostarczając tym samym metodę na uwzględnienie zmiennej tolerancji w równaniu zdolności procesu. Prawdopodobieństwo awarii jest obliczane poprzez wyznaczenie obszaru interferencji obu rozkładów. Pole interferencji dwóch rozkładów normalnych naprężenia i wytrzymałości można wyznaczyć z równania:
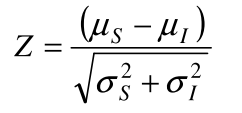
gdzie µI i σI są odpowiednio średnią i odchyleniem standardowym naprężenia a µS and σS są średnią oraz odchyleniem standardowym wytrzymałości.
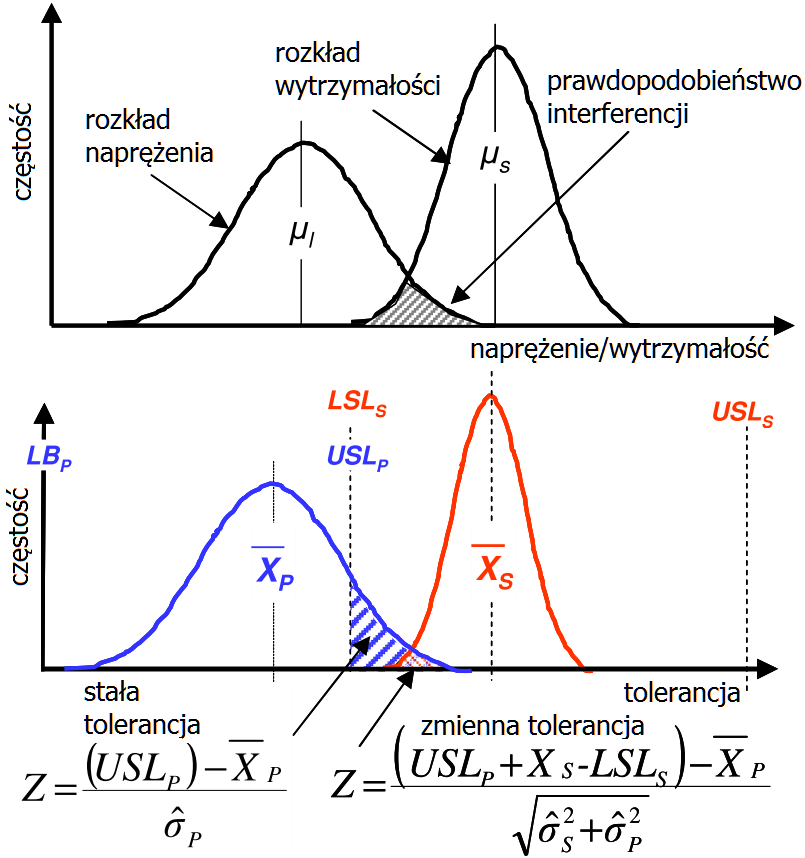
Analogicznie, prawdopodobieństwo wystąpienia wady w przypadku zmiennej tolerancji geometrycznej można znaleźć wyznaczając pole interferencji obu rozkładów – odchyłki geometrycznej i powiązanego z nią wymiaru. Wartość Z da się łatwo przekształcić na wskaźnik zdolności procesu Ppu dzieląc ją przez 3. Zgodnie z ciągłymi danymi zebranymi przez firmę TorqSmooth różnica między przewidywanymi zdolnościami wynosi:
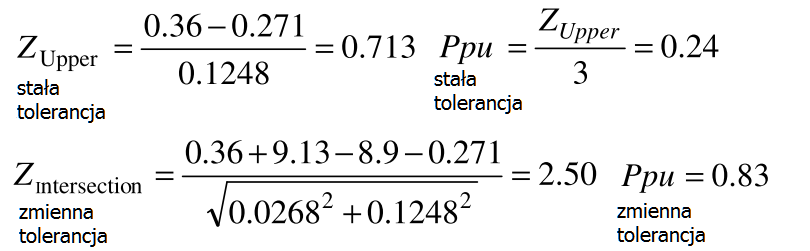
Prognozowanie zdolności procesu zwykle odbywa się poprzez porównanie części powierzchni pod krzywą rozkładu normalnego, która znajduje się powyżej USLP, do całkowitej powierzchni pod krzywą. Jednak sprawdzian atrybutywny porównuje całkowitą tolerancję (wyspecyfikowaną + bonus) każdej części z jej błędem pozycji. Wyjaśnia to dużą różnicę między przewidywanym poziomem niezgodności, który według TorqSmooth wyniesie aż 24% wyrobów, a faktycznym zerowym poziomem niezgodności stwierdzonym przez Aluminim Parts. Z powyższej analizy wynika, że rzeczywiste prawdopodobieństwo wady jest raczej bliższe stanowisku Aluminium Parts niż TorqSmooth. Z pewnością jednak nie wynosi ono 0%. Wartość ZUpper równa 0,713 w przypadku „stałej” tolerancji przekłada się na wskaźnik niezgodności wynoszący 23,79%, co oznacza, że w próbce 300 sztuk można oczekiwać 71,37 sztuk wadliwych (0,2379 * 300 = 71,37). Jeżeli jednak będziemy analizować „zmienną” tolerancję, wartość ZIntersection równa 2,5 przekłada się na wskaźnik niezgodności wynoszący 0,62%, czyli 1,86 wad na 300 sztuk. To że podczas sprawdzenia próbki 300 sztuk, nie wykryto żadnej wady, należy raczej przypisać niskiej wiarygodności kontroli atrybutywnej w porównaniu z pomiarem ciągłym, zwłaszcza gdy stosunek wyrobów zgodnych do niezgodnych jest bardzo wysoki.
Firma Aluminium Parts może uznać się za oczyszczoną z zarzutu, że 24% jej części jest wadliwych, ale w dalszym ciągu uzgodniony cel jakościowy na poziomie Ppk wynoszącego co najmniej 1,33 wydaje się być dosyć odległą perspektywą, szczególnie gdy do oceny wydajności procesu będą używane ciągłe dane pomiarowe. TorqSmooth może dalej żądać stuprocentowej kontroli atrybutywnej, aby mieć pewność, że utrzymywany jest minimalny poziom zdolności.
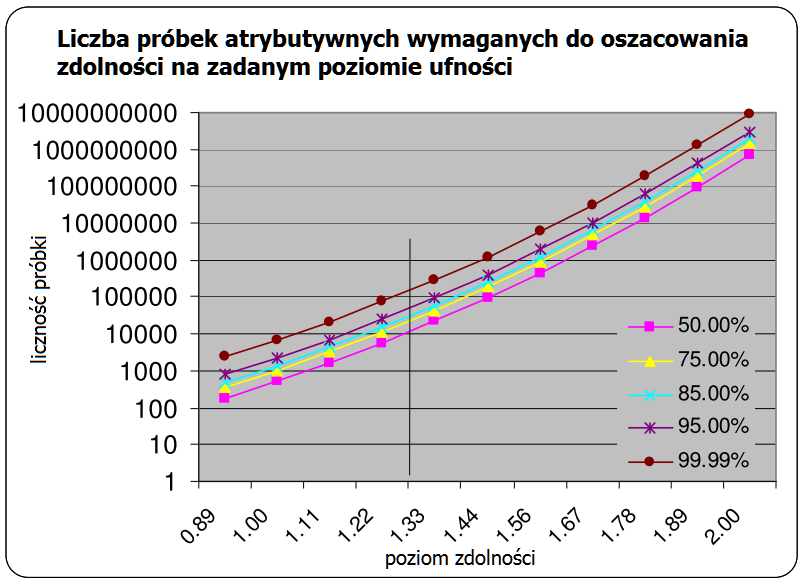
Z powyższego wykresu wynika, że nawet na poziomie ufności 50% rozmiar próbki w badaniu atrybutywnym, która potwierdzi poziom zdolności 1,33, musiałby być większy niż 10 000. Co więc powinna zrobić firma Aluminium Parts, aby udowodnić, że jej proces osiąga lepszą zdolność niż wymagane kryterium 1,33, lecz unikając kontroli wszystkich sztuk na sprawdzianach atrybutywnych? Poprawiono proces i zastosowano ciągłe dane pomiarowe do prognozowania jego wydajności!
Aluminium Parts zdecydowała, że zamiast sprawdzianów atrybutywnych do oceny każdej sztuki zostanie wprowadzona kontrola pomiarowa. Opracowano odpowiedni plan kontroli, a następnie użyto formuł do wyznaczania zdolności procesu z uwzględnieniem zmiennej tolerancji. Zdecydowano również o oddzielnym monitorowaniu współrzędnych pozycji X oraz Y, dzięki czemu nadzorowane zmienne będą odpowiadały podlegającym regulacji parametrom maszyny. Prowadząc oddzielną obserwację rozkładów zmiennych X i Y stwierdzono, że oba są normalne oraz „sterowalne”, ale nieznacznie przesunięte względem wartości docelowej. Wykres punktowy współrzędnych X i Y umożliwił wizualizację tych odchyłek. W rezultacie skorygowano rozkład każdej współrzędnej o wyznaczoną średnią odchyłkę X (-0,09) oraz Y (-0,06), a następnie ponownie przeliczono odchyłki pozycji, aby ocenić zdolność procesu po korekcie.
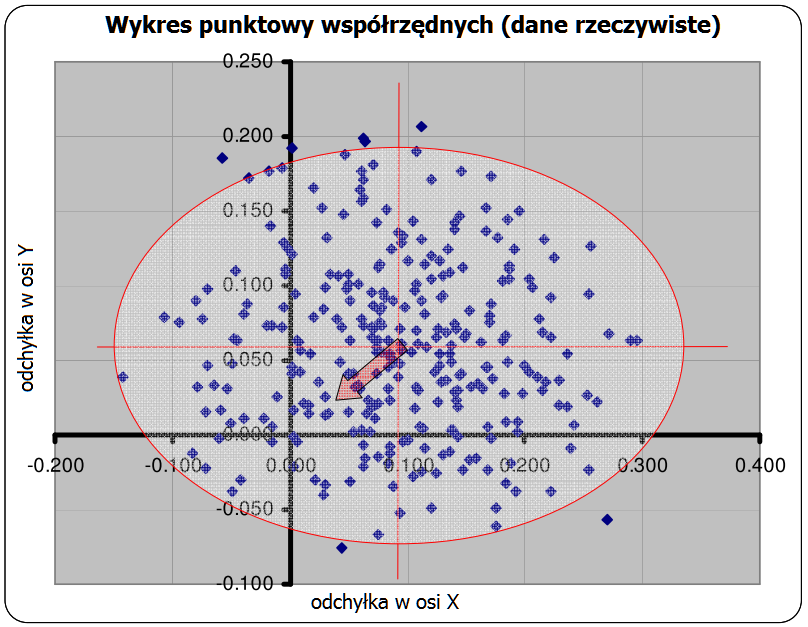
W firmie Aluminium Parts natychmiast dostrzeżono interesującą zmianę w przeliczonych pozycjach. Chociaż kształt rozkładu i zmienność poszczególnych współrzędnych pozostał bez zmian, kształt rozkładu odchyłek obliczonej pozycji zmienił się z przypominającego normalny na bardziej skośny, zaś jego odchylenie standardowe nieco spadło. Okazało się, że im bardziej wyniki dla poszczególnych współrzędnych są oddalone od celu, tym bardziej rozkład obliczonej odchyłki położenia przypomina rozkład normalny. Im zaś wartości współrzędnych są bliżej celu, tym większa ujawnia się skośność. Odkryto, że dzieje się tak, ponieważ obliczone odchyłki pozycji są zawsze dodatnie, z fizycznym ograniczeniem „w zerze”. Różna co do znaku, ale taka sama co do odległości odchyłka od celu wygeneruje taki sam dodatni wynik odchyłki pozycji. Ponieważ po skorygowaniu procesu pojawiło się więcej wartości współrzędnych blisko wartości docelowej, spowodowało to, że rozkład odchyłki zaczął wykazywać skośność w stronę docelowego „zera”.
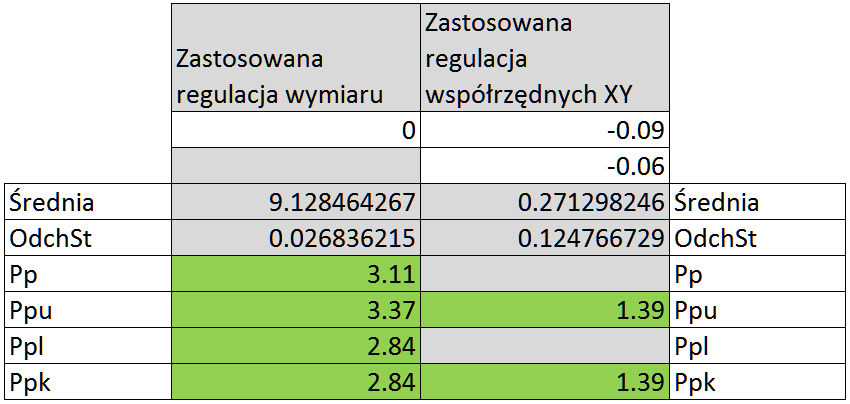
Poniższy histogram wskazuje, że dzięki skorygowaniu współrzędnych pozycji względem celu, nakładanie się obu rozkładów znacząco zmalało. Potwierdza to formuła obliczająca zdolność przy zmiennej tolerancji, która sygnalizuje wzrost zdolności Ppk wynoszącej pierwotnie 0,89 do 1,39 obecnie. Trzeba się jednak zastanowić, czy uzyskany wynik jest poprawny, ponieważ po regulacji normalny pozostał tylko rozkład wymiaru natomiast rozkład pozycji wykazuje brak normalności (skośność).
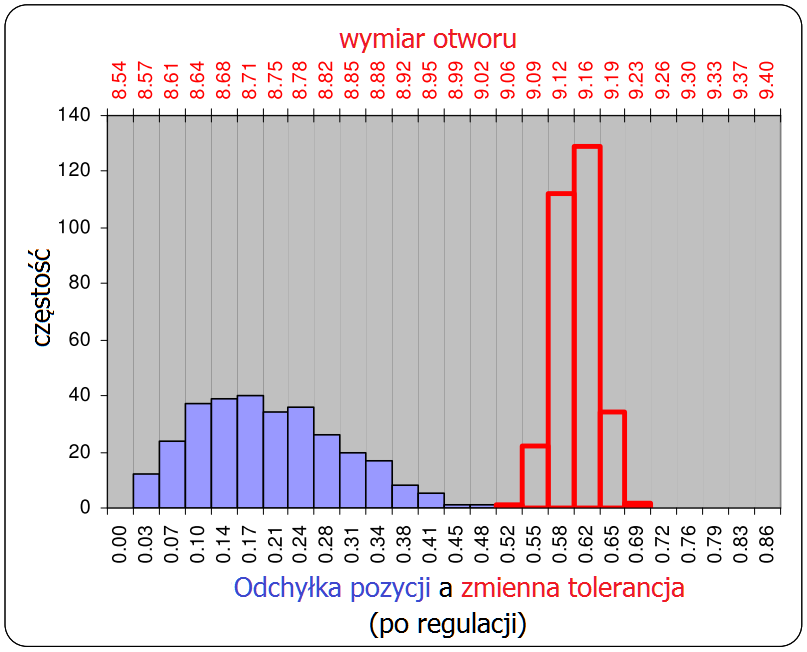
Aby oszacować błąd formuły dla zmiennej tolerancji firma Aluminium Parts zdecydowała się odtworzyć bardzo dużą próbkę skośnego rozkładu pozycji oraz zmiennej tolerancji, a następnie rozpatrzyć każdy przypadek w symulacji Monte-Carlo, aby uzyskać atrybutywny wynik „zgodny/niezgodny”, analogicznie do uzyskiwanego na sprawdzianie produkcyjnym. Następnie przewidywana wartością PPM sztuk wadliwych wynikająca z symulacji Monte-Carlo została porównana z przewidywaniami uzyskanymi dla „normalnych” danych ciągłych. Z wykresu Liczba próbek atrybutywnych… odczytano, że dla poziomu zdolności 1,39 i poziomu ufności 95% analizowana próbka powinna zawierać około 100 tysięcy wyników. Wygenerowano więc około 100 tysięcy losowych danych o rozkładzie normalnym, oddzielnie dla poszczególnych współrzędnych X i Y, przyjmując zaobserwowane odchylenie standardowe oraz średnią równą zero. Analogicznie wygenerowano dane losowe dla wymiaru, przyjmując zaobserwowaną średnią i odchylenie standardowe. Odchyłka pozycji w każdym wierszu została wyliczona według wzoru: 2*(X2+Y2)1/2, co spowodowało powstanie skośnego rozkładu pozycji. Następnie rozkład ten został porównany ze zmienną tolerancją pozycji, co dało atrybutywną statystykę „zgodny/niezgodny”. W symulacji na 100 tysięcy zbadanych próbek 73 zostały uznane za niezgodne (miały odchyłkę pozycji większą niż zmienna tolerancja).
Z poniższego wykresu porównującego wartość Ppk z wartością PPM wyrobów wadliwych możemy odczytać, że dla jednostronnie ograniczonego rozkładu normalnego współczynnik zdolności Ppk równy 1,39 powinien wykazać współczynnik wadliwości poniżej 32 PPM, natomiast symulacja Monte-Carlo wykazała, że poziom wadliwości PPM wyniesie 730, co z kolei odpowiada zdolności Ppk wynoszącej około 1,06.
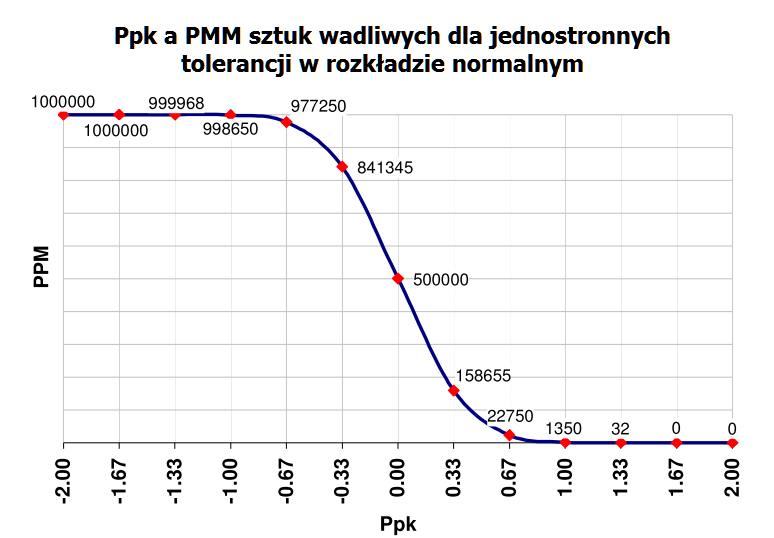
Niedoszacowanie wad, wynoszące 32 PPM w stosunku do 730 PPM, czyli (32-730)/1000000 = -0,07%, jest znaczące, lecz ten wynik i tak jest lepszy w porównaniu ze stosowaną dotychczas praktyką ignorowania zmiennej części tolerancji. Wystarczy go porównać z przeszacowaną wartością 24% wyrobów wadliwych, która wychodzi z obliczeń, jeżeli nie uwzględni się zmiennej tolerancji. Jeżeli jednak ten sam poprawiony „rozkład skośnej odchyłki wyśrodkowanej współrzędnej pozycji” zostałby przeanalizowany z uwzględnieniem zaawansowanej analizy dla rozkładów nie-normalnych, takiej jak transformacja Box-Cox, uzyskano by wynik Ppk równy 0,55, natomiast błąd oceny wadliwości w porównaniu do wyników ze sprawdzianu atrybutywnego wyniósłby (49350-730)/1000000 = 4,86% 2.
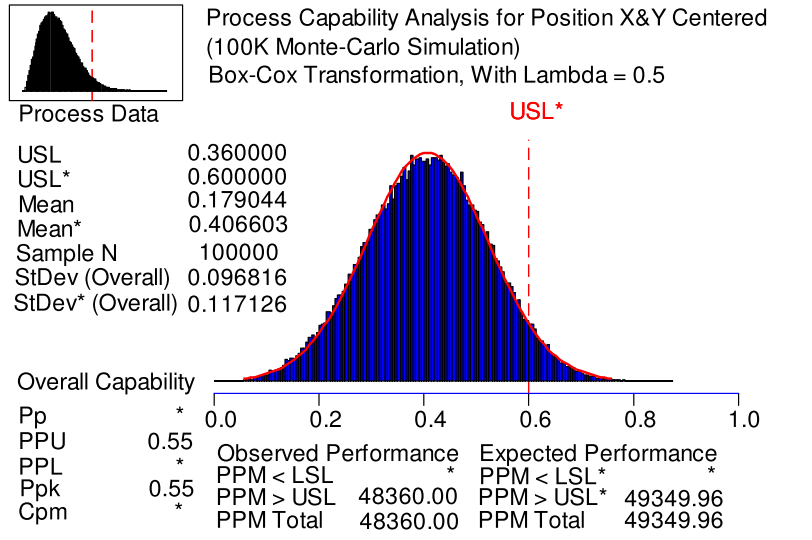
Okazuje się więc, firma Aluminium Parts wciąż ma problem, nawet po korekcie położenia rozkładu współrzędnych pozycji i zastosowaniu nowej formuły do oszacowania zdolności. Analiza monte-carlo wykazała, że Ppk wyniesie co najwyżej 1,06, podczas gdy TorqSmooth oczekuje wyniku 1,67 w fazie zatwierdzania PPAP oraz 1,33 w trakcie dalszej produkcji seryjnej.
Postanowiono jeszcze raz przyjrzeć się problemowi. Zauważono, że położenie rozkładu wymiaru otworu w obrębie jego granic specyfikacji bezpośrednio wpływa na ilość zmiennej tolerancji dostępnej dla pozycji otworu. Gdy tylko wymiar zbliża się do granicy MMC, zmienna tolerancja zmniejsza się i odwrotnie – gdy wymiar osiąga przeciwną granicę, zmienna tolerancja rośnie.
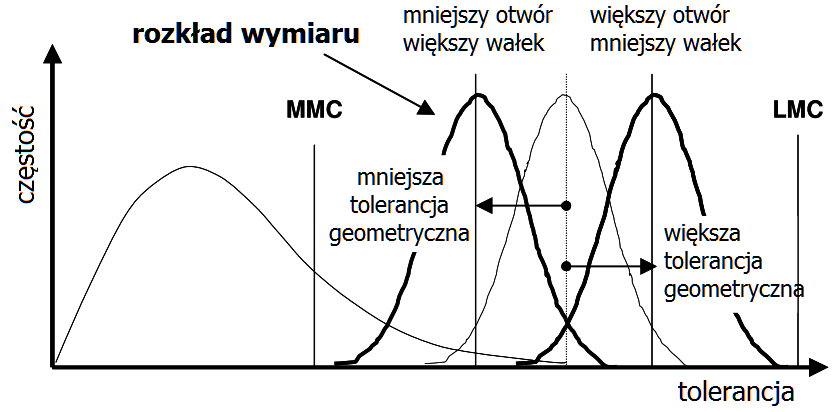
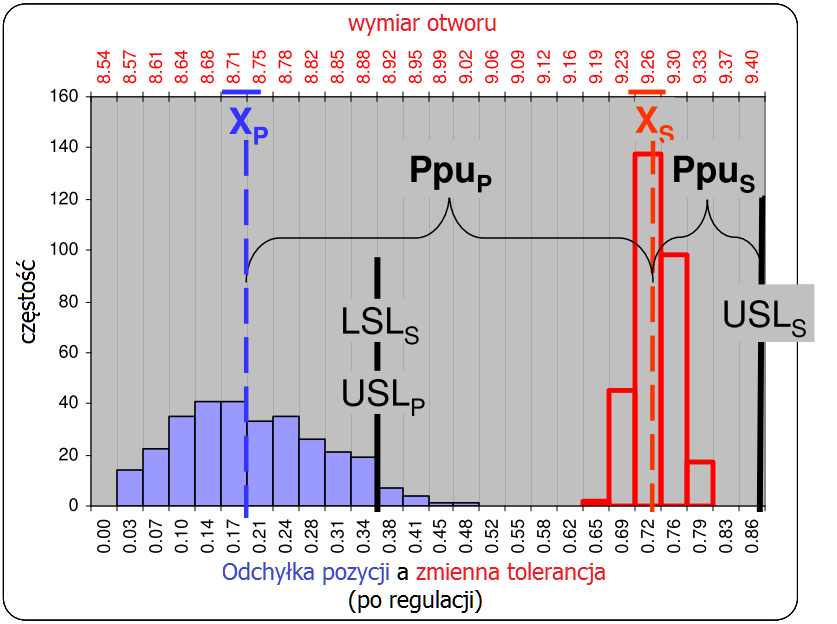
Tak się składa, że wymiar otworu jest parametrem, z którym Aluminium Parts ma najmniej problemów. Potencjał procesu Pp jest większy niż 3,0 a sam proces został zgodnie z regułami sztuki dobrze wyśrodkowany. Gdy więc chciano zwiększyć tolerancję pozycji, wystarczyłoby nieco zwiększyć średni wymiar otworu. Jednak jak bardzo, żeby z kolei nie zepsuć tej charakterystyki? Zbyt małe zwiększenie oznacza, że wartość pozycji jest bardziej narażona na przekroczenia górnej granicy specyfikacji, zaś zbyt duże podnosi ryzyko wad z tytułu przekroczenia USL wymiaru. Zdecydowano, że należy tak wyśrodkować wymiar otworu, aby prawdopodobieństwo wad zostało zminimalizowane jednocześnie obu charakterystyk. Zdano sobie sprawę, że jeżeli równania ZUpper P i ZUpper S zostaną przyrównane, w wyniku uzyska się optymalną wartość wymiaru utworu, przy której oba prawdopodobieństwa będą sobie równe.
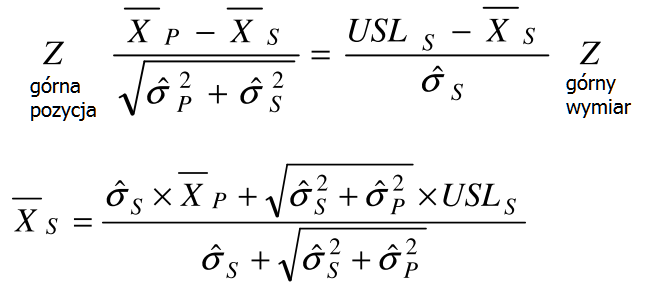
Aby znaleźć optymalny wymiar otworu, należy przetransformować średnią pozycji do odpowiadającego jej wymiaru otworu (0.18 +8.54) = 8.72

Po uzyskaniu wyniku wystarczy ponownie przetransformować optymalny wymiar otworu z powrotem na odpowiadającą mu średnią zmiennej tolerancji (9.254 – 8.54) = 0.714 i zastosować obie wartości w odpowiednich formułach zdolności:

Monitorując i kontrolując współrzędne pozycji X oraz Y oraz wyśrodkowując średni wymiar otworu na optymalnej wartości firma Aluminium Parts zwiększy swoje współczynniki zdolności do 1,81 i tym samym zredukuje współczynnik wadliwości do 27 ppb (parts per bilion).
Teraz pozostało już tylko jedno wyzwanie – trzeba przekonać firmę TorqSmooth, że chociaż wymiar otworu nie jest w środku specyfikacji a przy zastosowaniu tradycyjnej analizy zdolności proporcja wad pozycji otworu wydaje się być zbyt duża, to jednak można przewidywać, że prawdopodobieństwo napotkania wadliwej sztuki w tym procesie stało się ekstremalnie niskie.
Paul F. Jackson
Emerytowany inżynier rozwoju produktu, Ford Motor Company
Tłumaczenie: Piotr Stokłosa
__________
1 Ze względu na zachowanie spójności z rysunkami w wartościach specyfikacji oraz wynikach pomiarów pozostawiono kropkę jako separator liczb dziesiętnych. (przyp. tłum.)
2 Wynik uzyskany po transformacji Box-Cox dla danych pomiarowych uzyskanych po regulacji współrzędnych X/Y lecz bez uwzględniania „bonusu” wynikającego ze zmiennej tolerancji. (przyp. tłum.)