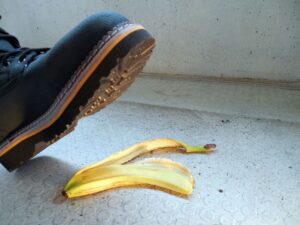
FMEA – Analiza potencjalnych wad i ich skutków to jedno z podstawowych narzędzi planowania pod kątem analizy ryzyka w projektowaniu wyrobu i procesach produkcyjnych. Należy pamiętać, że analiza FMEA nie jest narzędziem istniejącym samodzielnie, lecz stanowi integralną część procesu zaawansowanego zapewniania jakości APQP. Wejściem do analizy FMEA powinny być charakterystyki specjalne zidentyfikowane na podstawie specyfikacji klienta jak i własnej znajomości procesu oraz schemat przepływu procesu (flow chart). Z kolei wyjściem z FMEA powinien być plan kontroli (Control Plan).
Dokumenty te, czyli schemat przepływu, FMEA oraz plan kontroli powinny tworzyć spójny, zintegrowany zestaw. Nieprzypadkowo więc często nazywa się je „trylogią APQP”. Co więcej, FMEA powinno być żywym dokumentem, w którym gromadzona jest wiedza o napotkanych i rozwiązanych problemach dotyczących zarówno projektu jak i procesu produkcyjnego. W tym celu konieczne jest również angażowanie w tworzenie FMEA zespołów interdyscyplinarnych. Dopiero pełna wiedza z różnych obszarów organizacji oraz zapewnienie różnych punktów widzenia daje szansę na uzyskanie miarodajnej analizy ryzyka.
Czytaj więcej:
Szkolenie w formie warsztatów, polegających na opracowywaniu dokumentacji procesowej dla przygotowanych przez uczestników szkolenia przykładów procesów realizowanych w organizacji. Szkolenie ma na celu zapoznanie uczestników z zasadami tworzenia dokumentacji procesowej: Process Flow Diagram/Chart + PFMEA + Control Plan, według najnowszych wytycznych przemysłu motoryzacyjnego, przedstawienie najlepszych praktyk, wykonaniu dokumentacji procesowej dla wybranych przez uczestników operacji z wartością dodaną, logistycznej i kontrolnej oraz przeprowadzenie dynamicznej oceny dokumentacji przygotowywanej przez uczestników podczas warsztatów. Wymagania przemysłu motoryzacyjnego co do dokumentacji procesowej. Powiązania pomiędzy dokumentami. Podejście procesowe w przygotowaniu schematu przepływu procesu (PFD). Wyrób jako suma charakterystyk produktowych. Elementy PFD/PFC i rola schematu w ujęciu
Analiza ryzyka staje się coraz powszechniej stosowanym narzędziem w systemach zarządzania jakością. Dobrze przeprowadzona i utrzymywana pozwala zminimalizować koszty złej jakości. Podstawowym narzędziem stosowanym w tym zakresie w motoryzacji (i nie tylko) jest analiza FMEA. Występuje ona obecnie w wielu odmianach, z których najpopularniejsze to analiza ryzyka w projektowaniu wyrobu (Design FMEA) oraz analiza ryzyka w procesach (Process FMEA). Analiza FMEA Analiza FMEA to technika analityczna zapewniająca, że potencjalne problemy w procesie projektowania wyrobu i jego wytwarzania są odpowiednio zidentyfikowane i zarządzane w ramach całego cyklu APQP. Kluczowym elementem dobrej analizy FMEA jest poprawne zastosowanie metodologii, dobór odpowiedniego zespołu oraz przeprowadzenie
Pojęcia takie jak error-proofing, mistake-proofing czy poka-yoke są powszechnie używane w języku przemysłu motoryzacyjnego. Gdy mowa jest o błędach występujących w procesie i metodach zapobiegania im oraz ich wykrywania, panuje bałagan wyrażeń, pojęć i znaczeń. Na skutek licznych naleciałości, wewnętrznych „standardów” organizacji (standardów w cudzysłowie, bo raczej należałoby mówić o naturalnie wykształconym języku plemiennym) pojęcia te są często mylone, stosowane wymiennie lub całkowicie błędnie interpretowane. Warto więc przyjrzeć się dokładniej definicjom, które w odniesieniu do tych i innych pojęć proponuje zarówno podręcznik AV FMEA jak i sama norma IATF 16949. Zacznijmy od pojęć podstawowych. Często dostaję pytania dotyczące analizy błędów: co rozumieć
FMEA (Failure Mode and Effects Analysis) czyli analiza rodzajów błędów oraz ich skutków polega na analitycznym ustalania związków przyczynowo-skutkowych powstawania potencjalnych wad produktu oraz uwzględnieniu w analizie czynnika krytyczności (ryzyka). Jej celem jest konsekwentne i systematyczne identyfikowanie potencjalnych wad produktu/procesu, a następnie ich eliminowanie lub minimalizowanie ryzyka z nimi związanego. W branży motoryzacyjnej na podstawie IATF 16949 obowiązkowe jest prowadzenie analizy DFMEA (analiza ryzyka konstrukcji produktu) oraz PFMEA (analiza ryzyka procesu wytwarzania produktu). Częstym podejściem jest rozbicie procesu wytwarzania na dwa etapy: proces produkcyjny, w którym są analizowane wszystkie operacje dodające wartość produktowi oraz proces logistyczny związany z dostarczeniem surowców
Po rewolucji związanej z audytami przejścia na IATF 16949:2016, w branży motoryzacyjnej szykuje się kolejne BUMM, którym będzie połączenie dotychczas używanych podejść do tworzenia FMEA (ang. Failure Mode and Effect Analysis), takich jak AIAG i VDA 4. Mimo, iż autorzy obiecują dwuletni okres ujednolicenia, pojawia się wiele wątpliwości. Czy ten czas będzie wystarczająco długi? Co z analizami, które są na etapie aktualizacji, czy trzeba będzie przeprowadzić je jeszcze raz? W tej chwili dysponujemy tylko szkicem przyszłego standardu, który nie jest ostateczną wersją. Czytając ten dokument możemy stwierdzić jednoznacznie, że stanowczo łatwiej będzie przejść ze standardu VDA niż AIAG. Sześciostopniowy algorytm