Po rewolucji związanej z audytami przejścia na IATF 16949:2016, w branży motoryzacyjnej szykuje się kolejne BUMM, którym będzie połączenie dotychczas używanych podejść do tworzenia FMEA (ang. Failure Mode and Effect Analysis), takich jak AIAG i VDA 4. Mimo, iż autorzy obiecują dwuletni okres ujednolicenia, pojawia się wiele wątpliwości.
Czy ten czas będzie wystarczająco długi? Co z analizami, które są na etapie aktualizacji, czy trzeba będzie przeprowadzić je jeszcze raz? W tej chwili dysponujemy tylko szkicem przyszłego standardu, który nie jest ostateczną wersją. Czytając ten dokument możemy stwierdzić jednoznacznie, że stanowczo łatwiej będzie przejść ze standardu VDA niż AIAG. Sześciostopniowy algorytm realizacji metody do złudzenia przypomina co najmniej trzy z pięciu kroków VDA. Dodatkowo dochodzi do tego etap definiowania i powoływania zespołu. Osoby realizujące FMEA według podejścia VDA świetnie zdają sobie sprawę, iż bardzo trudno realizuje się trzy pierwsze kroki bez odpowiedniego, dedykowanego narzędzia, ponieważ program Excel może już nie wystarczyć. Ważne żeby w tym okresie rozpoznać potrzeby i zdefiniować trudności, które mogą się pojawić po opublikowaniu połączonej wersji FMEA przygotowanej przez AIAG i VDA.
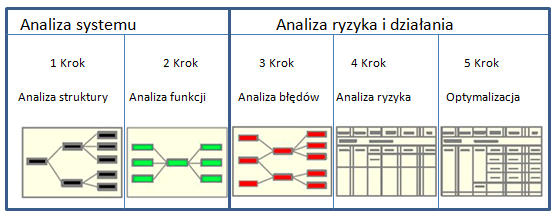
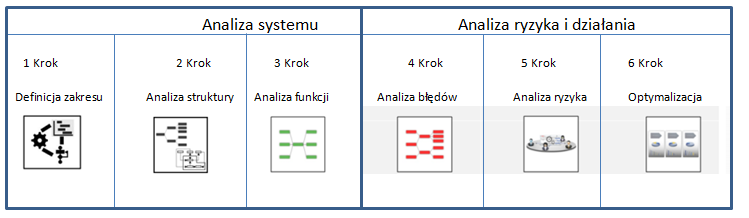
Według VDA 4 pierwszym krokiem jest Analiza struktury drzewa. Przykład struktury drzewa procesu znajduje się na rys 1. Etap ten polega na zdefiniowaniu wszystkich podzespołów produktu (DFMEA) lub kroków procesowych w przypadku PFMEA oraz przyczyn, które mogą na nich wystąpić.
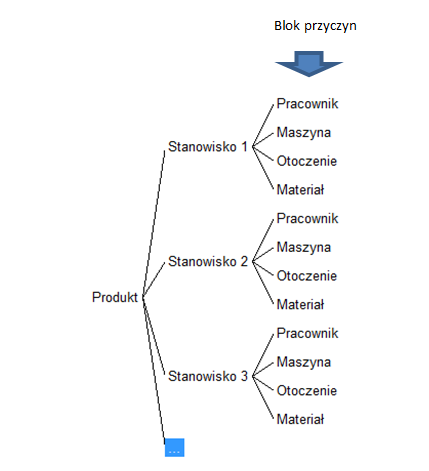
Następnym krokiem według VDA 4 jest analiza sieci funkcji. Przykładowa sieć funkcji znajduje się na rys. 2. Etap ten polega na powiązaniu: w przypadku DFMEA charakterystyk podzespołów z charakterystykami produktu oraz wpływem na oczekiwania klienta i użytkownika; W przypadku PFMEA na połączeniu funkcji pracowników, parametrów procesu, parametrów otoczenia z charakterystyką produktu oraz wpływem na oczekiwania klienta, użytkownika i wewnętrzny proces.
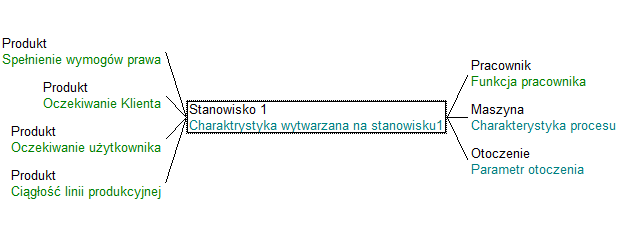
Kolejny krok według VDA 4 to analiza sieci błędów, która jest wykonana na podstawie poprzedniego kroku analizy funkcji. Przykładową sieć błędów pokazano na rys. 3. Analiza ta jest najistotniejszym etapem tworzenia arkusza FMEA. Polega na połączeniu kolejnych błędów z przyczynami po prawej stronie oraz nie spełnieniem wymagań klienta, użytkownika (DFMEA i PFMEA) lub procesu wewnętrznego (PFMEA).
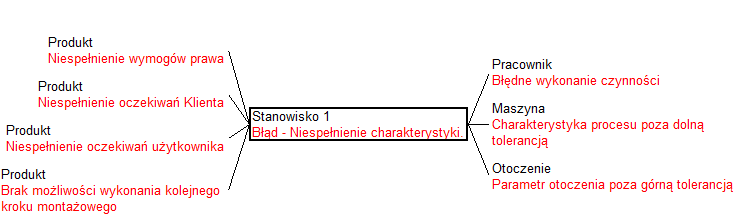
Przeprowadzenie powyższych kroków analizy za pomocą programu Excel jest możliwe ale bardzo pracochłonne. Dodając do tego liczbę godzin, którą trzeba poświęcić na analizę, zdefiniowanie działań prewencyjnych i detekcyjnych oraz na późniejszą optymalizację ryzyka, a następnie wymnażając ten czas przez liczbę osób, które należą do interdyscyplinarnego zespołu tworzącego FMEA, otrzymamy niebagatelną sumę. Od razu w myśl filozofii Lean pojawia się pytanie: jak ją zmniejszyć? Odpowiednie narzędzie w postaci programu wspomagającego tworzenie FMEA oraz odpowiednia znajomość algorytmu tworzenia będą pomocne w optymalizacji tego czasu.