Jedną z podstawowych zasad, którą stosuję w pracy z zespołami, jest ustalenie, czy pojęcia których używamy, rozumiemy w podobny sposób. Wprowadziłam ją, gdy pewnego razu po godzinnym spotkaniu ze swoim zespołem projektowym zorientowałam się, że nasze nieporozumienia w dużej mierze wynikają z zupełnie innego definiowania pojęć, które są podstawą naszej zawodowej codzienności. Jednym z takich pojęć jest „jakość”. Dlatego wszystkie spotkania zespołowe zaczynam od pozornie niewinnego pytania: Czym dla Was jest jakość?
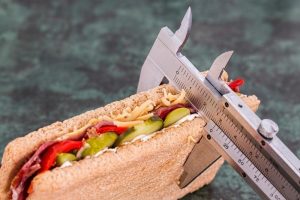
Zawsze jestem zaskoczona, jak wiele różnych odpowiedzi wtedy pada. Poza oczywistą definicją zaczerpniętą z normy, pojawia się mnóstwo autorskich koncepcji, co dowodzi, że pojęcie jakości jest bardzo różnie rozumiane.
A wydawałoby się, że skoro jest to drugie po „ilości” najczęściej wypowiadane słowo w zakładach produkcyjnych, to wszyscy powinniśmy mieć na myśli to samo.
Skąd więc bierze się ta niejednoznaczność?
Pewnie stąd, że samo słowo jakość będzie w zasadzie pozbawione istotnego znaczenia, dopóki nie określimy, czego ta jakość ma dotyczyć. Tak samo jak sama „długość” nie może być oceniona, dopóki nie wiemy o długości czego mówimy.
Jeżeli w procesie wytwarzania sprecyzujemy, że „mówimy o jakości wyrobu” lub „pracujemy nad jakością procesu”, temat będzie zdecydowanie bardziej jednoznaczny i dopiero upewniając się, że wszyscy mówimy i myślimy o tym samym, możemy dyskutować o tym, czym jest świadomość jakościowa.
Pochylmy się najpierw nad jakością wyrobu i zadajmy sobie pytanie, jakie narzędzia służą do budowania świadomości jakościowej w tym zakresie? Musimy sprecyzować, w jakich procesach budowana jest świadomość jakości wyrobu/produktu i kiedy zaczyna się proces ustalania jakości wyrobu? Oczywiście w procesach przygotowania procesu produkcyjnego, podczas projektowania wyrobu. Proces ten nazywamy procesem planowania jakości (Quality Planning). Podstawowe narzędzia używane na tym etapie narzucane są bardzo precyzyjnie przez normę IATF 16949, zaliczamy do nich takie metody jak amerykańska APQP (Advanced Product Quality Planning) czy niemiecka RGA (Reifegradabsicherung) zwana też MLA (Maturity Level Assurance).
To w pierwszych etapach zaawansowanego planowania jakości wyrobu budowana jest jego jakość, poprzez precyzyjne zidentyfikowanie oraz dokładne przełożenie charakterystyk funkcjonalnych na charakterystyki produktowe oraz poprzez wyłonienie charakterystyk specjalnych. Można więc powiedzieć, że świadomość jakości produktu to świadomość istnienia w wyrobie charakterystyk, szczególnie charakterystyk specjalnych.
Jakie narzędzia wykorzystujemy do budowania świadomości jakości procesu? Wszystkie narzędzia wykorzystywane podczas planowania procesu muszą skupiać się na charakterystykach specjalnych: zidentyfikowane charakterystyki specjalne wyrobu muszą przełożyć się na charakterystyki specjalne procesowe i być widoczne zarówno w schemacie przebiegu procesu, analizie ryzyka, planie nadzoru ale przede wszystkim w instrukcjach i szkoleniach, których utworzenie i przeprowadzenie jest celem całego procesu planowania jakości.
Zadajmy sobie pytanie: czy na poszczególnych etapach planowania jakości mamy świadomość jakości wyrobu i procesu? Czy znamy wszystkie charakterystyki specjalne wyrobu i procesu? Czy potrafimy dokładnie określić, które z nich i w jaki sposób wpływają na bezpieczeństwo, które na spełniane funkcje, a które na montowalność? Czy wiemy, jak je będziemy nadzorować i ewentualnie kontrolować?
Jak chcemy budować świadomość jakościową wśród pracowników operacyjnych, skoro sami jej nie posiadamy, skoro nie zbudowaliśmy podwalin świadomości jakości produktu i procesu na fundamentalnym etapie budowania jakości, czyli podczas planowania jakości?
Jeżeli jednak Wasza odpowiedź brzmi – Tak, jestem świadom wszystkich charakterystyk specjalnych produktowych i procesowych, znam ryzyka związane z produkcją tych charakterystyk, wiem jakie działania muszę prowadzić by zabezpieczyć proces przed popełnianiem błędów, które poskutkowałyby wyprodukowaniem wady – to możemy przejść do następnego etapu procesu jakościowego. Jest nim oczywiście … proces zapewnienia jakości (Quality Assurance).
Na czym polega ten proces i jakie narzędzia wspomagają nasze wysiłki w tym etapie procesu jakościowego?
Oczywiście wszelkiego rodzaju instrukcje i idące za nimi (ZAWSZE!) szkolenia – to podstawowe narzędzia jakościowe, które stosujemy na linii produkcyjnej. Służby budujące i wzmacniające świadomość jakościową na tym etapie procesu jakościowego powinny nosić koszulki z napisem: „W czym Ci mogę pomóc?” bo ich rolą jest rozwiewanie wszelkich wątpliwości operatorów co do wykonywanych czynności. To modne (znowu po latach) szkolenia wewnątrz organizacji (TWI – Training Within Industry), odprawy jakościowe, rozmowy z pracownikami (MBWA – Management By Walking Around), wizualizacja (np. alerty jakościowe), itp. To praca w cyklu PDCA, więc przede wszystkim wyciąganie wniosków z efektywnego rozwiązywania problemów.
To również wszelkie zaplanowane narzędzia prewencyjne, w tym standaryzacja i wszelkiego rodzaju rozwiązania jakości wbudowanej w proces, np. rozwiązania błędoodporne (Error Proofing), statystyczne metody sterowania procesem (SPC – Statistical Proces Control), systemy sygnalizujące błędy procesowe (typu andon), systemy zabezpieczające proces produkcyjny przed błędami konfiguracyjnymi, narzędzia szczupłego wytwarzania (LM – Lean Manufacturing). Wszystkie te narzędzia powinny zostać zaplanowane w procesie planowania jakości, poddane analizie ryzyka i wdrożone, aby na etapie produkcji służyć zapewnieniu jakości i podlegać już „tylko” nadzorowi.
Ostatnim etapem jakości jest jej kontrola (Quality Monitoring). Tę rolę powinniśmy ograniczyć do minimum, a najlepiej całkowicie wyeliminować. Ale skoro poprzednie dwa procesy jakościowe nie są naszą najlepszą stroną (a właściwie patrząc na rozbuchane systemy kontrolne w zakładach musiałabym stwierdzić, że raczej są naszą słabością) to niestety marnotrawimy czas i pieniądze na coś, co jest całkowicie zbędne czyli kontrolujemy jakość. O narzędziach w tym procesie nie będę mówić, bo tu Wasza kreatywność nie zna granic. Potraficie doskonale przeprowadzać i optymalizować coś, czego w ogóle nie powinniśmy wykonywać. J
Wszystkie trzy role procesu jakościowego: planowanie, zapewnienie oraz kontrolowanie składają się na proces zarządzania jakością (Quality Control) i to zarządzanie, sterowanie czy nadzorowanie chciałabym podkreślić. Naszym obowiązkiem jest zabezpieczyć system przed wyprodukowaniem wady, a nie ją wykrywać (ISO9001) i taką świadomość jakościową powinniśmy budować i wzmacniać.