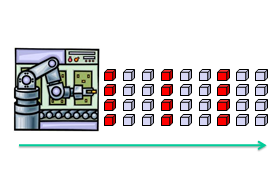
Statystyczne sterowanie procesem nie może ograniczać się do jednorazowej oceny jego zdolności na początku produkcji seryjnej (co niestety często ma miejsce), ale powinno mieć charakter ciągły (ang. ongoing process monitoring). Oznacza to, że zdolność procesu należy oceniać przez cały czas trwania produkcji. Pod tym ogólnym stwierdzeniem kryje się znacznie szerszy temat – jak często i w jakiej ilości próbkować proces, aby zapewnić jego wiarygodną ocenę, a sprowadzając zagadnienie do poziomu czysto operacyjnego: „z jaką częstotliwością i w jakiej ilości pobierać próbki z procesu?”.
Na wstępie załóżmy najprostszy możliwy scenariusz, niestety występujący relatywnie rzadko – produkcja ma charakter ciągły, tzn. przez dłuższy okres czasu produkowany jest ten sam detal na tych samych nastawach maszyny. Taki charakter produkcji występuje np. w tłoczniach, gdzie przezbrojenia maszyn są zbyt kosztowne czasowo i organizacyjne, by produkować krótkimi seriami; dotyczy to również zakładów specjalizujących się w produkcji kilku typów detali dla jednego klienta. Zauważyłem już, że taki scenariusz jest najprostszy, ponieważ produkcja ma charakter masowy i długotrwały, co pozwala obserwować niezakłócane przezbrojeniami zachowanie się procesu w dłuższym przedziale czasu. Tego typu procesy są „najwdzięczniejszym” obiektem do zastosowań SPC – długotrwała obserwacja pozwala na wychwycenie i opanowanie głównych źródeł zmienności a wynikłe z tego regulacje jednoznacznie przekładają się na poprawę jakości produkcji.
Jednak nawet w tym najprostszym scenariuszu w dalszym ciągu pojawia się pytanie: jak często badać proces (czyli jak często pobierać próbkę) oraz jak duża ma ona być (ile sztuk ma być mierzonych)? Po pierwsze przybliżenie odpowiedzi sięgnijmy do źródeł, a konkretnie do podręcznika Statistical Process Control [1].
Wielkość podgrupy
W przypadku badania zdolności procesu za pomocą wskaźników Cp i Cpk jak również w przypadku prowadzenia kart kontrolnych XR, próbki pobierane są w tzw. podgrupach. Oznacza to, że co pewien czas (czyli z pewną częstotliwością) z procesu pobieranych jest n, najczęściej kolejno wyprodukowanych sztuk. Ponieważ sztuki te były produkowane w krótkim przedziale czasu (w stosunku do częstotliwości próbkowania – np. wyprodukowano je w ciągu 5 minut, podczas gdy próbkowanie odbywa się co 2 godziny), uzyskane z nich pomiary tworzą podgrupę. Ze względu na sposób wyliczania współczynników Cp i Cpk oraz prowadzenia karty XR dane powinny być tak rejestrowane, aby było wiadomo, do której podgrupy należą. W praktyce produkcyjnej podgrupy zawierają od 2 do 5 pomiarów, wykonanych na takiej samej ilości sztuk (1 pomiar na 1 sztuce).
Jeżeli chodzi o ilość danych wystarczających do statystycznej oceny procesu, w podręczniku [1] znajdziemy następujące sformułowanie: Do sprawdzenia stabilności procesu przyjmuje się, że należy zebrać co najmniej 25 podgrup zawierających łącznie 100 lub więcej pomiarów. Oznacza to, że należy zebrać co najmniej 25 podgrup po co najmniej 4 pomiary, co jest wystarczające, aby ocenić stabilność, a następnie zbadać położenie i rozrzut procesu [1], a więc również ocenić jego zdolność. Te zalecenia bardzo często są rozszerzane w wymaganiach specyficznych klientów, na przykład w wymaganiach VW znajdziemy zapis: Liczność podgrupy musi wynosić co najmniej 3 (zalecane 5) [2], natomiast całkowity rozmiar próbki powinien być większy od 125 (liczba podgrup * liczność podgrupy) [2].
Mamy więc wytyczne minimum, nie jest to jednak odpowiedź na pytanie, jak należy postępować później, tzn. gdy już wstępna zdolność procesu zostanie oceniona na podstawie wspomnianych 100 lub 125 pomiarów? Niestety, nie znajdziemy tu gotowych procedur ani wzorów. Powód tej sytuacji jest zasadniczy – w realnym procesie produkcyjnym występuje zbyt wiele zmiennych, aby można stworzyć uniwersalną formułę wyliczającą częstość próbowania i liczność podgrup. Dlatego podręcznik [1] nie podaje w tej kwestii konkretów, stwierdzając jedynie, że należy przyjąć podgrupy o racjonalnej liczności, tzn. takiej, która minimalizuje szansę wystąpienia przyczyny specjalnej w podgrupie, ponieważ kluczowym celem jest porównanie zmienności w obrębie podgrup ze zmiennością między podgrupami. Dalej pojawia się również propozycj\, aby na początku procesu stosować podgrupy o większej liczności, a jeżeli zaobserwowane przesuwanie się procesu jest niewielkie, stopniowo przechodzić na mniej liczne. Jak widać, w tych zaleceniach nie znajdziemy konkretnych wartości. Mimo to, opierając się na opisanych wcześniej wymaganiach do oznaczania wstępnej zdolności procesu, w przemyśle przyjęło się, że wyjściową wartością jest podgrupa o liczności 5, którą następnie zmniejsza się do 3 lub nawet 2 pomiarów.
Częstotliwość próbkowania
czyli częstotliwość, z jaką z procesu pobierana jest próbka; na przykład, jeżeli sztuki do pomiarów pobierane są co 2 godziny, mówimy, że „częstotliwość próbkowania” wynosi 2 godziny.
Jak już wspomnieliśmy, klienci wymagają od swoich dostawców monitorowania procesów „na bieżąco”. Wynika stąd, że jednorazowa ocena stabilności i zdolności procesu na początku produkcji jest niewystarczająca. Niesatysfakcjonujące są również kontrole wyrywkowe, polegające na doraźnej ocenie procesu co jakiś czas (i znowu pytanie – co jaki?). Idealny scenariusz z punktu widzenia oceny procesu będzie więc polegał na tym, że jest on próbkowany przez cały czas jego trwania. Jeżeli np. produkcja danego detalu odbywa się w systemie ciągłym przez okres 1 roku, to proces powinien być oceniany na przestrzeni tego roku.
Pojawia się więc kolejne pytanie: Jak często powinniśmy pobierać próbki? Jaka powinna być częstotliwość próbkowania? Czy wystarczy próbkować raz na miesiąc, raz na tydzień, raz dziennie, raz na zmianę, co dwie godziny, co jedną? Również w tym przypadku podręcznik SPC [1] nie daje jednoznacznej odpowiedzi, stwierdzając tylko, że częstotliwość próbkowania powinna być na tyle „gęsta”, aby wyłapać zmiany pojawiające się w procesie wraz z upływem czasu. Krótko mówiąc, odpowiedzialność za dobór częstotliwości próbkowania spoczywa na inżynierach procesu i technologach, znających swoje procesy, ich szybkość (czas cyklu) oraz podatność na zmiany. Na przykład jest oczywiste, że rzadziej będzie próbkowany proces, w którym wytwarza się jedną sztukę co 10 minut a częściej proces „wypluwający” cztery sztuki na sekundę. Analogicznie, jeżeli z doświadczenia wiemy, że proces długoterminowo utrzymuje wysokie wskaźniki zdolności, znacznie powyżej wymagań klienta (np. osiągane jest Cpk=2,5 przy wymaganym Cpk>1,33), to częstotliwość próbkowania również może być znacznie zmniejszona, ponieważ ryzyko wyjścia poza specyfikację jest relatywnie małe.
Autorzy podręcznika [1] zwracają również uwagę, aby opracowując plan próbkowania uwzględnić czynniki mogące generować zmienność w procesie, na przykład: zmianowość (a więc przynajmniej raz na zmianę), zmęczenie operatora (a więc kilka razy w ciągu zmiany), trendy wynikające z nagrzewania się urządzeń, różne partie komponentów itp.
Oczywiście zderzają się tu dwa cele – z jednej strony chcemy jak najlepiej poznać i nadzorować proces (a więc próbkować go jak najczęściej), z drugiej jednak dążymy do minimalizacji wysiłku i kosztów związanych z pomiarami (rzadsze próbkowanie). Musimy więc znaleźć złoty środek, podobnie jak w przypadku liczności podgrup. Montgomery [4] sugeruje, że we współczesnej praktyce przemysłowej występuje tendencja do tworzenia mniejszych podgrup, ale zbieranych częściej. Dodatkową pomocą w rozstrzygnięciu wspomnianego konfliktu są coraz częściej występujące systemy pomiarów automatycznych, na stałe zaimplementowane w procesie. W tym przypadku pomiar nawet 100% wyrobów i prowadzenie SPC na całej populacji jest stosunkowo mało kosztowne.
Ciekawą propozycją mogą być też zalecenia sformułowane przez E.Dietricha i A. Schulza [3] oraz poszerzone o kilka moich sugestii:
Wyższa częstotliwość próbkowania | Niższa częstotliwość próbkowania |
proces niestabilny, mała zdolność (Cpk na poziomie 1,33) | proces stabilny i/lub wysoka zdolność (Cpk>>2.5) |
charakterystyka krytyczna dla funkcji lub procesu | charakterystyka niekrytyczna dla funkcji lub procesu |
nowa technologia produkcji | znana technologia produkcji |
brak doświadczeń | duże doświadczenia |
krótki czas życia narzędzia | długi czas życia narzędzia |
oczekiwanie wysokiego poziomu istotności statystycznej | wysoka istotność statystyczna nie jest wymagana |
wymagana możliwość szybkiej reakcji w celu wykrycia części wadliwych lub wątpliwych | wystarczająca reakcja „na czas” w przypadku wystąpienia części wadliwych lub wątpliwych |
szybki proces (krótkie czasy cyklu) | wolny proces (długie czasy cyklu) |
częste przezbrojenia | rzadkie przezbrojenia |
Wspierając się powyższymi zaleceniami oraz polegając na własnym doświadczeniu mamy duże szanse, że dobrana częstotliwość próbkowania będzie optymalna – umożliwi odpowiednio szybką reakcję na niekorzystne zmiany w procesie nie angażując przy tym nadmiernych środków na działania kontrolne.
Literatura:
[1] Statistical Process Control, AIAG, Lipiec 2005
[2] VW 101 31, Process Capability Investigation for Measurable Characteristics, VW, Luty 2005
[3] E. Dietrich, A. Schulze „Statistical Procedures for Machine and Process Qualification”, Hanser, 2010
[4] D.C. Montgomery, „Introduction to Statistical Quality Control”, Wiley, 2009