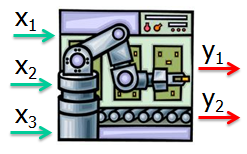
W przemyśle motoryzacyjnym jest stosowanych wiele narzędzi rozwiązywania problemów jakościowych. Każde z nich ma swój najlepszy obszar zastosowań. Występują również zróżnicowane podejścia do rozwiązywania problemów, definiowane w specyficznych wymaganiach klienta.
Wśród tych metod jest dostępne szczególne narzędzie, przydatne przy rozwiązywaniu problemów powodowanych przez wiele czynników jednocześnie. Jest nim analiza DoE (Design of Experiment), umożliwiająca analizowanie wpływu różnych czynników na wyrób i wzajemnie na siebie.
Każdy z własnego doświadczenia może potwierdzić, że niewiele jest problemów, które da się wyjaśnić jedną przyczyną. W rezultacie często spotykamy się z twierdzeniem, że procesu nie można ustawić, ponieważ wpływają na niego „tysiące parametrów”. Czy jednak jest możliwe, aby proces był zależny od tak dużej liczby parametrów? Zdecydowana większość z nich jest pochodną innych parametrów. Parametry zależne od innych nie mają bezpośredniego wpływu na proces. Wymagane jest więc zrozumienie tych zależności.
DoE wykorzystywane jest do określania wpływu parametrów wejściowych procesu na wyjście procesu. Dzięki tej analizie możemy ustalić, jak silny jest wpływ poszczególnych parametrów na wyjście. Analiza daje również możliwości określenia oddziaływania pomiędzy parametrami wejściowymi. Jak już wspomniałem, często zdarza się, że zmieniając jeden parametr, możemy wpływać na wartość innego. Mówimy wówczas, że parametry są od siebie zależne.
Analiza DoE nie jest zbyt często wykorzystywana, ponieważ jej przeprowadzenie wiąże się z dość długim procesem, na który składają się:
- Ustalenie parametrów wejściowych – najtrudniejsza część, gdyż zbyt duża liczba rozpatrywanych parametrów znacznie wydłuży eksperyment, ale z drugiej strony zbytnie ograniczenie może doprowadzić do błędnych wniosków.
- Ustalenie wartości MAX i MIN parametrów wejściowych – takie ustalenie poziomów parametrów, które uważamy za możliwe, bądź w zakresie dopuszczalnych zmian. Wartości te mogą być ustawiane w sposób płynny (lub stopniowo) a także atrybutywno, tzn. możemy ustawić np. materiał typu A dla stanu MAX i materiał typu B dla stanu MIN, lub też smarowanie dla stanu MAX i brak smarowania dla stanu MIN.
- Zaplanowanie eksperymentu – w jaki sposób będziemy przeprowadzać eksperyment. Ważne jest systematyczne podejście do przeprowadzenia eksperymentu, ponieważ jego złożoność i chaotyczne przeprowadzanie może spowodować wydłużenie eksperymentu albo uzyskanie błędych wyników, a w konsekwencji niewłaściwych wniosków.
- Przeprowadzenie eksperymentu – to zwykle najdłuższa część Czas eksperymentu wydłuża się w zależności od ilości zdefiniowanych parametrów wejściowych. A każdy eksperyment należy kilkukrotnie powtórzyć. Za eksperyment uważa się przeprowadzenie badania (np. wyprodukowanie sztuki) przy jednym ustawieniu parametrów.
- Przeanalizowanie wyników – najtrudniejsza faza eksperymentu. Właściwa inetrpretacja wyników to klucz do sukcesu, a założenie o ich poprawności i braku błędów w przeprowadzanym eksperymencie jest kluczowe.
- Ustalenie wpływu parametrów wejściowych – końcowe ustalenie parametrów przeprowadzonego eksperymentu, które mają największy wplyw na wyjście procesu.
- Ustalenie wartości parametrów wejściowych, które będą utrzymywać proces w wymaganej specyfikacji – takie ustalenie wartości tolerancji dla wybranych parametrów, by wyjście procesu dawało zadawalające nas wyniki jakościowe.
Nie jest to więc proces krótki. Tym bardziej, że właściwa interpretacja wyników nie należy do oczywistych i nie generuje samonasuwających się wniosków dla eksperymentatora przeprowadzającego takie doświadczenie po raz pierwszy.
Analiza DoE występuje również w wielu wariantach, do których zaliczamy:
- Analiza wyjść procesu – wykorzystanie kart kontrolnych. Właściwa interpretacja kart kontrolnych daje możliwości ustalenia zmienności występujących procesie. Na podstawie kart można określić, czy dana maszyna bądź narzędzie mają wpływ na proces. Każde narzędzie może produkować różniące się pomiędzy sobą wyroby, co sztucznie może zwiększać zmienność procesu. Zidentyfikowanie takich zachowań jest prostą metodą na ograniczenie zmienności procesu.
- Porównywanie parami – porównywanie pomiędzy sobą wyrobów o odmniennej jakości, tej która jest jak najlesza i tej która jest zdecydowania zła. Takie porównywanie w szybki sposób może dostarczyć odpowiedzi, a na pewno nasunąć pytania, dlaczego dobry wyrób nie stanowi problemu, a co jest takiego w niezgodnym wyrobie, że jest nie spełnia on wymagań.
- Zamiana elementów – tam gdzie wyrób składa się z montowanych razem wielu składowych elementów, do analizy brane są wyroby o najwyższej jakości i te niespełniające wymagań, przy czym systematycznie wymieniane są ich elementy składowe, a następnie jest badana jakość wyrobu po takiej wymianie. Takie działanie pozwala szybko ustalić, który element ma wpływ na analizowany problem. Ten typ analizy przy rozwiązywaniu problemów jest często wykonywany nieświadomie i przez to ułamkowo. Jednak każdy z nas z pewnością może wymienić kilka przykładów, kiedy zajmując się rozwiązywaniem problemu analizował wpływ składowych elementów wyrobu obserwując jego zachowanie.
- Zamiana czynników – tam gdzie na wartość charakterystyki wyrobu ma wpływ kilka charakterystyk procesu, jak np. prędkość przesuwu, temperatura czynnika chłodzącego, typ narzędzia frezującego, materiał narzędzia, materiał obrabianego elementu, itd. Ustalane są czynniki, określany jest ich wpływ na jakość wyrobu po zamianach ustawień czynników i wybierane te, które mają największy wpływ na jakość procesu.
Ze względu na ilość eksperymentów przeprowadzaną dla parametrów wejściowych analizę DoE dzieli się na:
- Analizę pełną – wykonywane są wszystkie możliwe kombinacje ustawień parametrów wejściowych z ich wartościami ustawień. Analiza daje pełny obraz zależności parametru wyjściowego od parametrów wejściowych oraz oddziaływań pomiędzy nimi. Jednak wraz z rosnącą ilością parametrów i chęcią sprawdzenia ich wartości (niekoniecznie musi to być zawsze MAX i MIN, można również sprawdzić wartości pośrednie) ilość kombinacji rośnie wykładniczo, co znacznie wydłuża eksperyment, który przecież musi być powtórzony kilkukrotnie.
- Analizę ułamkową – wykonywane są nie wszystkie kombinacje ustawień parametrów wejściowych z ich wartościami ustawień, a tylko te, które zapewniają warunek tzw. ortogonalności, czyli ilość pomożonych przez siebie ustawień parametrów wejściowych na określonych poziomach dla dowolnych dwóch kolumn musi być sobie równa.
Dla chcących rozszerzyć podstawową wiedzę z zakresu planowania eksperymentów polecam rozdział w książce „Zarządzanie jakością z przykładami” Adama Hamrola rozdział 5.2.3 DOE – planowanie eksperymentów strony 241-268, na podstawie której, opracowałem plik w excelu dla przeprowadzania analizy zamiany czynników. Plik jest w maksymalnym stopniu zautomatyzowany i na podstawie przeprowadzonych eksperymentów sam podaje wpływy parametrów wejściowych. Plik pobrać można ze strony w części download. Wspomniana książka zawiera wiele przykładów. Dla każdej opisywanej procedury przedstawiono praktyczne rozwiązania, dzięki czemu jest ona wartościową pozycją w biblioteczce inżyniera.